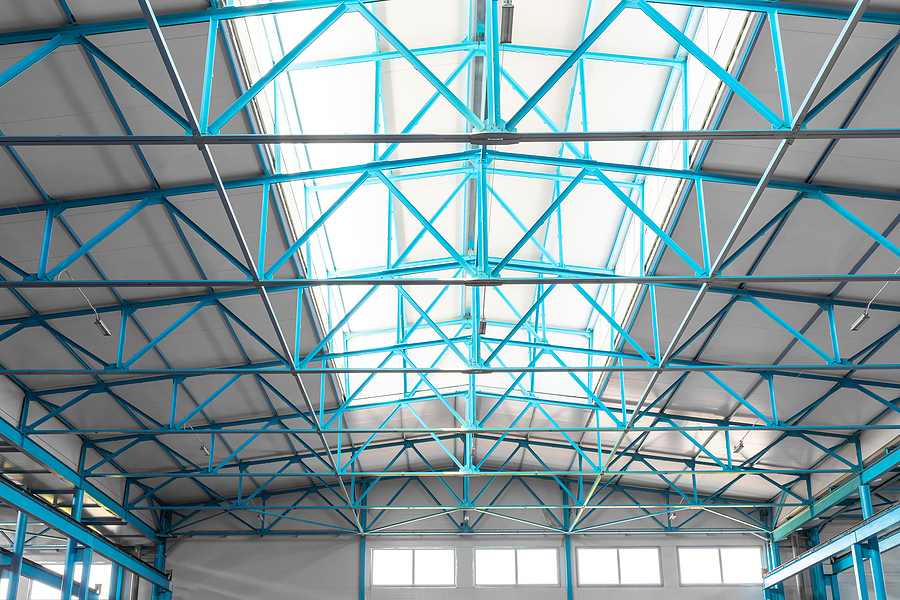
Modular Buildings vs Prefab – What the Difference?
Modular buildings and prefabricated (prefab) buildings are both types of off-site construction, where components or units of the building are produced in a factory and then assembled or installed on-site. However, there are key differences in the way these methods are applied.
Modular Buildings:
Modular buildings are comprised of multiple sections, or “modules,” which are individually constructed in a factory environment before being transported to the site. Each module typically includes a significant portion of a building, such as an entire room, and can include internal fittings and fixtures.
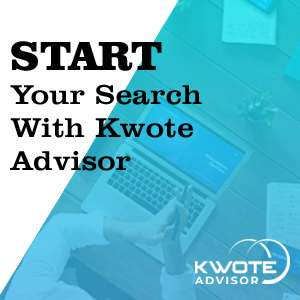
The modules are then arranged and connected on-site to form a complete building, according to the building’s design. This method can offer significant time savings as site preparation can be done concurrently with the module construction. Once the modules are assembled on site, the building often looks no different than a building constructed entirely on-site.
Examples of Modular Buildings:
- Housing: Residential buildings, including single-family homes and multi-story apartment buildings, can be constructed using modular methods. Each room, or a set of rooms, is built as a separate module, then transported to the site and assembled.
- Hotels: The hospitality industry has adopted modular construction due to the speed of construction and the ability to repeat designs. Each hotel room can be identical and made in a factory setting, improving quality control.
- Hospitals and Healthcare Facilities: Modular construction is used to build fully equipped patient rooms, operating rooms, and diagnostic labs, which can then be transported to the site and connected to the main building.
- Office Buildings: Modular construction can be used to build office spaces, with individual offices, conference rooms, and other common areas each made as a module.
Prefabricated Buildings:
Prefabrication, or prefab, is a construction method where specific components of a building, such as walls, floors, or roof trusses, are built in a factory, then transported to the construction site and assembled. Unlike modular buildings, prefab construction often involves only parts of a building rather than whole rooms or sections.
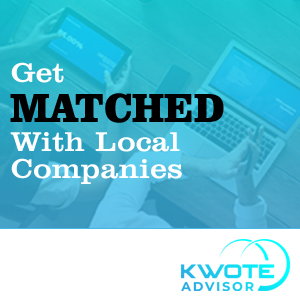
Prefab construction allows for a high degree of customization, as different components can be mixed and matched on-site to create a wide range of building designs. It also offers time and cost savings, as well as improved quality control over traditional construction methods, but generally not to the same degree as modular construction.
Examples of Prefabricated Buildings:
- Homes: A lot of prefab homes exist where certain parts like roof trusses, floor panels, and wall sections are created in a factory and then assembled on-site.
- Commercial Buildings: Prefab methods are often used in the construction of commercial buildings. For instance, the structural steel that forms the skeleton of a high-rise building might be fabricated off-site and then erected on-site.
- Schools and Classrooms: Prefabricated classrooms are becoming popular due to the speed of construction and cost-effectiveness. Various components of the classroom, such as the walls and roof, are built off-site and then assembled on-site.
- Garden Sheds or Studios: Smaller structures like garden sheds, home offices, or artist studios are often prefabricated. The components are made in a factory, delivered as a kit, and then quickly assembled on-site.
While both modular and prefabricated buildings leverage off-site construction for efficiency and quality control, the key difference lies in the extent of the off-site construction. Modular construction involves building large, complete sections of a building, while prefab construction involves creating individual components that are assembled on-site.
Advantages and Disadvantages Modular Buildings vs Prefab Buildings
Let’s examine the advantages and disadvantages of both modular and prefabricated buildings:
Modular Buildings
Advantages:
- Time Efficiency: Since modules are constructed simultaneously in a factory while site preparation is being done, the construction time is greatly reduced compared to traditional methods.
- Quality Control: Building in a controlled factory environment allows for better quality management and consistency. There’s less chance of construction errors, and problems can be fixed before the modules arrive at the construction site.
- Reduced Waste: Since construction occurs in a controlled environment, there’s less waste produced as materials are used more efficiently and can be recycled within the factory setting.
- Less Disruption: On-site work is minimized, reducing the noise, dust, and disruption to the surrounding community.
Disadvantages:
- Transportation Limitations: There may be logistical challenges in transporting large modules, especially to remote or congested urban locations. The module size might be limited by what can be transported.
- Design Limitations: Although the modules can be combined in various ways, there may be some design limitations compared to traditional construction methods.
- Perception and Resale Value: Some people may perceive modular buildings as lower quality, which could potentially affect the resale value of the property. However, this perception is changing as the quality and design possibilities of modular buildings continue to improve.
Prefabricated Buildings
Advantages:
- Cost and Time Efficiency: Like modular construction, prefab construction can result in reduced construction time and cost savings due to the controlled factory environment.
- Flexibility: Prefab offers a high degree of customization as different components can be mixed and matched on-site to create a wide range of building designs.
- Quality Control: The controlled factory environment allows for improved quality control, less waste, and better use of materials.
Disadvantages:
- Design Limitations: Even though prefab offers more flexibility than modular, there can still be design constraints compared to on-site construction.
- Transportation and Assembly: Transporting prefab components requires careful handling to prevent damage. The assembly of these components on-site also requires skilled labor and precision.
- Dependent on Site Preparation: Prefab construction relies more on the site being ready, as the construction process is more linear than with modular buildings. Weather conditions can still delay the building process.
In both cases, the advantages can outweigh the disadvantages, particularly when the project is well-planned and the construction process is managed effectively. The key is to choose the most suitable method based on the specific requirements and constraints of each project.
Cost Comparison: Modular Buildings vs. Prefabricated Buildings
When it comes to contemporary construction methods that prioritize efficiency, speed, and environmental sustainability, modular and prefabricated (or prefab) buildings often top the list. Both offer unique benefits and come with their distinct cost factors. By examining these costs, construction planners and prospective homeowners can make informed decisions based on their project needs and budgets.
Modular Buildings: A Cost Overview
Modular buildings are constructed off-site in controlled factory settings where entire rooms or sections of the building are created. Once assembled on-site, the structure can often be indistinguishable from a building constructed using traditional methods.
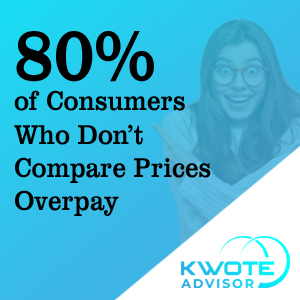
From a cost perspective, modular construction can offer significant savings due to several key factors:
- Time Efficiency: The simultaneous construction of the building modules in a factory while the site is prepared can dramatically reduce the overall construction timeline. Shorter construction times can reduce financing costs, labor costs, and allow for faster occupancy, which is particularly beneficial for commercial projects.
- Reduced Waste: The controlled factory environment allows for precision, leading to less material waste and more efficient use of resources. The ability to recycle materials within the factory further enhances cost-efficiency.
- Consistent Quality: Improved quality control can result in fewer on-site corrections, leading to a smoother construction process and potentially lower costs in the long run.
However, it’s important to note that modular buildings may face additional transportation and logistical costs due to the need to transport large modules to the site.
Prefabricated Buildings: A Cost Perspective
Prefabricated buildings also involve off-site construction, but rather than entire sections, individual components like walls, roofs, or floors are manufactured. These are then assembled on-site to complete the building.
Prefab buildings also offer potential cost savings:
- Cost and Time Efficiency: Similar to modular construction, prefab construction can lead to lower labor costs and reduced construction time. However, the level of efficiency might be lower than in modular construction as the process is more linear.
- Less Material Waste: Prefabrication also offers the advantage of less waste due to the controlled factory environment, resulting in cost savings.
- Economies of Scale: If many similar components are needed, mass production can lead to economies of scale, lowering the cost per unit.
On the downside, the transportation of prefabricated components requires careful handling, which can potentially increase costs. Additionally, assembly on-site needs skilled labor and precision, and any delays in site preparation can lead to increased costs.
While both modular and prefab construction methods offer potential cost savings, the extent and nature of these savings can vary depending on specific project requirements, design complexity, site conditions, and local labor and material costs. It’s crucial to work closely with experienced architects, builders, and cost consultants who can provide accurate cost estimates and guide informed decision-making. As construction methods continue to evolve, these cost dynamics may also change, reflecting new innovations and efficiencies in the sector.